In today’s rapidly evolving world, the food and beverage industry is constantly seeking sustainable solutions to meet the growing demands of production, address the challenges of aging infrastructure, and comply with stringent environmental regulations. Pretreatment processes play a crucial role in achieving these goals by enhancing the efficiency and effectiveness of various applications.
Wastewater Pretreatment Applications
Many industries have some level of wastewater pretreatment ahead of their own full wastewater treatment plant (WWTP) or before discharging to the local Publicly Owned Treatment Works (POTW.) This not only protects the municipal treatment facility but also helps industries remain compliant with environmental regulations.
Screening and Grit Removal
Screening is the first line of defense in a pretreatment system. It involves removing large solids—such as food scraps, packaging remnants, and plastics—from the wastewater stream, typically with rotary drum screens, stair screens or bar screens. These materials can be recovered for further processing and their removal also helps prevent clogged pipes and damage to downstream equipment.
Grit removal targets smaller, abrasive materials like sand and other fine particles that are harmful to downstream equipment. Vortex and cyclone style grit removal systems are commonly used.
Equalization (EQ) Basins
EQ basins help balance fluctuations in both the flow rate and the concentration of pollutants in wastewater. By collecting and slowly releasing wastewater at a steady rate, EQ tanks ensure that downstream processes — like biological treatment or chemical dosing — operate under more consistent and optimized conditions.
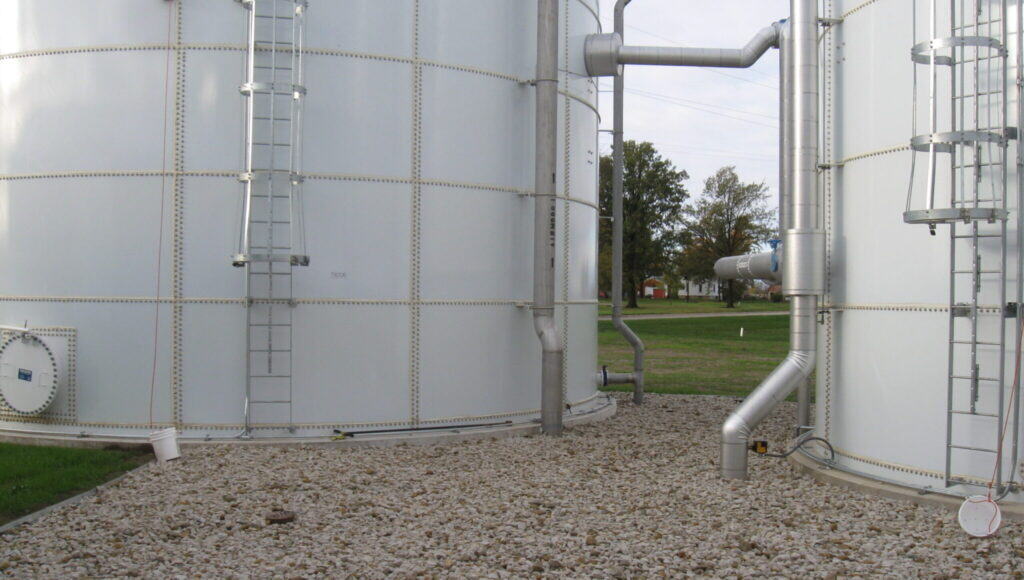
FOG, TSS, and BOD Removal
Many industrial processes in food and beverage manufacturing generate wastewater with high levels of fats, oils, and greases (FOG), total suspended solids (TSS), and biochemical oxygen demand (BOD). Low density wastewater, FOG in particular, is difficult to treat and can form blockages and interfere with downstream biological processes. Solids separation by flotation can remove up to 90% of Suspended Solids, including FOG, BOD and other colloidal materials
1. DAF – Dissolved Air Flotation
DAF is a widely used technology that uses pressurized or aspirated air to create microbubbles. These attach to FOG and suspended solids, lifting them to the surface for removal. The DAF process is enhanced by conditioning the incoming waste stream with appropriate pH adjustment, coagulation, and flocculation.
2. SAF – Suspended Air Flotation
The SAF process is very similar to a DAF configuration but instead of microbubbles it introduces a surfactant-based froth directly into the wastewater stream. It offers advantages such as a smaller footprint, higher loading rates, lower operating costs, and charged bubbles to attract floc.
pH Adjustment
Industrial processes can result in acidic or alkaline wastewater that must be neutralized before discharge. Chemical feed systems add acids or bases—like sulfuric acid or sodium hydroxide—to bring the pH into the acceptable range. Flash mixing zones optimize chemical effectiveness and minimize chemical use.
Biological Treatments
Biological processes are often used in pretreatment of high strength wastewater prior to discharge to a conventional WWTP or POTW but are also utilized in full treatment systems. They use microorganisms to break down organic pollutants. These systems can be aerobic or anaerobic, depending on the nature of the wastewater.
1. Anaerobic Systems
Anaerobic wastewater treatment is a method of treating wastewater that relies on microorganisms that thrive in oxygen-free environments to decompose organic matter. It can significantly reduce BOD and chemical oxygen demand while generating biogas as a byproduct. Common systems include lagoons and high-rate anaerobic reactors. It can also be used as a pretreatment step before aerobic treatment.
2. Activated Sludge
Activated Sludge systems use oxygen to facilitate microbial consumption of organic matter and nitrification of ammonia, as well as anoxic and anaerobic selectors to facilitate biological nutrient removal. Technologies like Biological Nutrient Removal (BNR), Membrane Bioreactor (MBR), and Sequencing Batch Reactors (SBR) are commonly used for the core treatment process for BOD and nutrient removal.
3. Sedimentation and Clarification
This physical process is integral to activated sludge and facilitates heavier solids to settle at the bottom of a tank for removal. Chemicals like Alum and Ferric Chloride or polymers are often used to bind smaller particles into larger aggregates for enhanced settling.
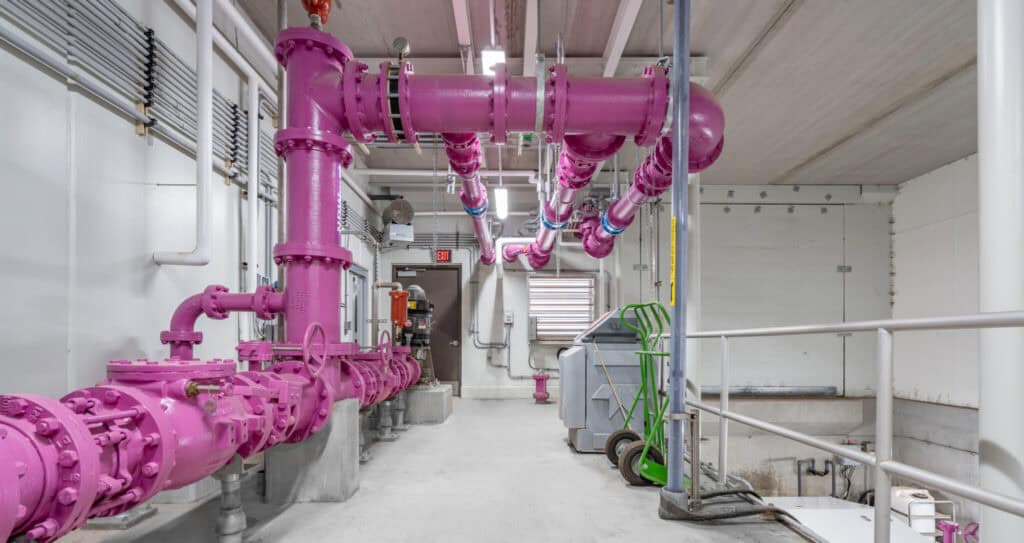
Common Challenges in Wastewater Pretreatment for Food and Beverage
In the food and beverage industry, wastewater pretreatment faces several common challenges, including aging infrastructure, retrofitting within limited footprints, and maintaining continuous operation during construction sequencing.
Aging Infrastructure
Aging infrastructure presents a growing challenge for food and beverage manufacturers managing wastewater treatment. Many treatment systems in this sector were originally built decades ago and may not be equipped to handle modern processing demands or comply with increasingly stringent regulatory requirements.
Retrofitting Within a Limited Footprint
Upgrades commonly require retrofitting existing infrastructure within a limited footprint. Most food and beverage manufacturing facilities are space-constrained, especially older ones or those in urban or suburban settings.
Construction Sequencing
Construction sequencing is crucial to maintaining continuous WWTP operation. Sequencing involves the careful planning and coordination of construction activities to ensure the treatment system remains functional and compliant during upgrades or retrofits.
Optimal Pretreatment Offers Multiple Benefits
A well-designed and properly maintained pretreatment system offers multiple benefits, including:
- Reduces loading on downstream processes: By removing solids, FOG, and high-strength organics early, pretreatment systems decrease the biological load on main treatment processes. This allows for smaller aeration basins, lower energy consumption, reduced chemical dosing and sludge handling needs, improved equipment lifespan, and lower maintenance.
- Improves operational stability of downstream units: Pretreatment smooths out variations in flow and load, helping downstream systems operate within optimal parameters.
- Increases compliance with effluent limitation guidelines (ELGs): Pretreatment helps meet ELG parameters more reliably, reducing dependency on advanced polishing systems.
- Reduces risk of fines and surcharges: Pretreatment minimizes the likelihood of violating discharge permits or exceeding limits set by POTWs.
- Enables resource recovery opportunities:
- Biogas generation: High-strength organics captured in pretreatment can be directed to anaerobic digesters to produce methane-rich biogas for energy generation or heat recovery.
- Water reuse: Cleaner effluent from pretreatment improves the efficiency of reuse systems, making treated water suitable for non-potable reuse such as cleaning, irrigation, or cooling.
- Byproduct recovery: Solids and residuals from pretreatment can sometimes be processed into marketable or beneficial products such as animal feed or fertilizer. For example, the captured FOG from a DAF or SAF can be sold as an ingredient for pet food or as tallow to a rendering company.
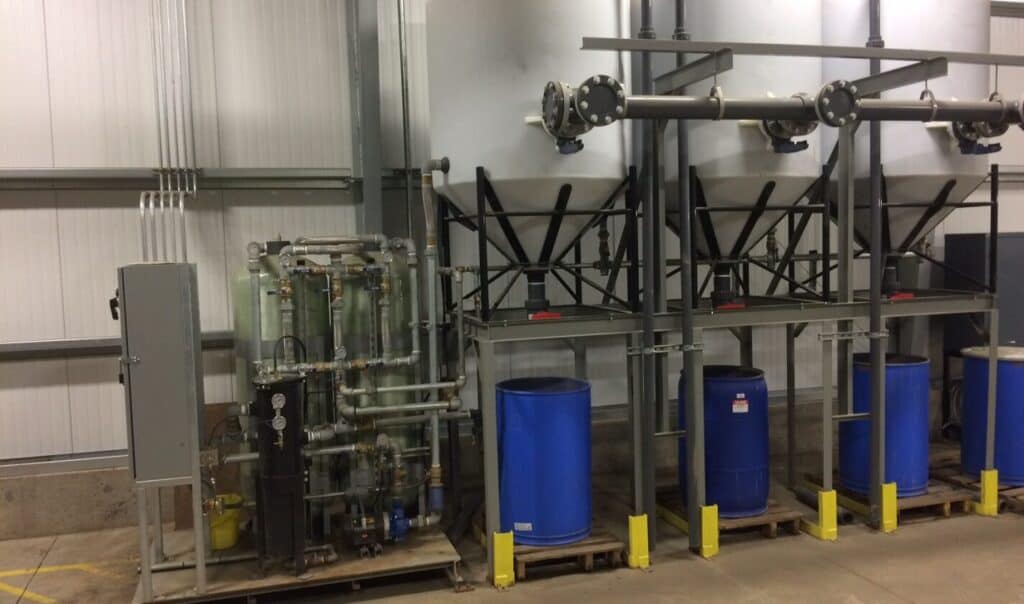
New Technologies Can Increase Capacity Within the Same or Smaller Footprint
Modern treatment technologies are designed to be more efficient, compact, and scalable than older traditional systems. This allows food and beverage manufacturers to significantly increase their treatment capacity without requiring large physical expansions. These technologies include:
- Membrane Bioreactors: A proven technology in both municipal and industrial settings, MBRs combine biological treatment and membrane filtration in a compact system. They offer a smaller footprint than conventional activated sludge systems and produce high-quality effluent suitable for reuse.
- Process Intensification and Densification: Emerging technologies are advancing the treatment of industrial waste, enhancing settling performance, and improving nutrient removal capabilities at existing facilities.
- High-rate Anaerobic Systems: Systems such as upflow anaerobic sludge blankets or expanded granular sludge bed reactors treat high-strength wastewater efficiently and produce biogas, all in relatively small volumes.
- Skid-mounted or Containerized Treatment Systems: These systems allow rapid deployment and require less on-site construction and space.
- Automation and Monitoring Technologies: Smart sensors can reduce manpower requirements, optimize process control, and reduce the need for oversized equipment to handle variability.
HR Green’s Professionals Partner with You to Design Smarter Pretreatment Strategies
Implementing a well-planned pretreatment system protects public infrastructure, maintains regulatory compliance, and can significantly reduce operational costs. Investing in the right pretreatment technologies is a smart, sustainable choice.
If you’re exploring pretreatment options or upgrading your current system, our industrial water team can help design a solution tailored to your needs. Contact us today to learn how we can help you optimize your pretreatment strategy.